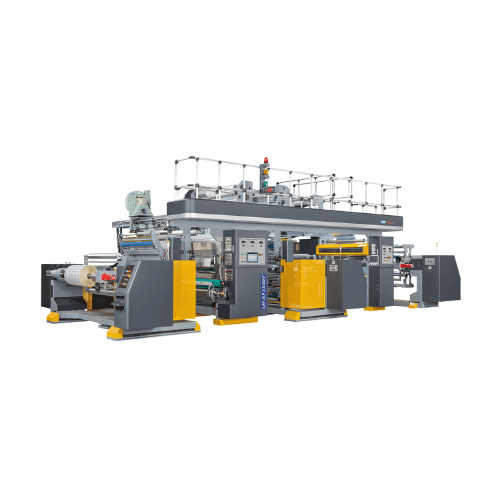
雙軸無溶劑貼合機LM-SF1300T
產品分類 : 工業覆膜/塗佈機
- 無軸式收放料 - 雙軸回璇收、放料座 - 塗膠座 四輪獨立傳動式塗膠系統,包含測量輪、給膠輪、轉印輪椅及塗膠輪 - 轉印輪 套筒式轉印輪 輕量且快速更換 - 不停機自動接紙系統 減少換軸過程中的材料浪費
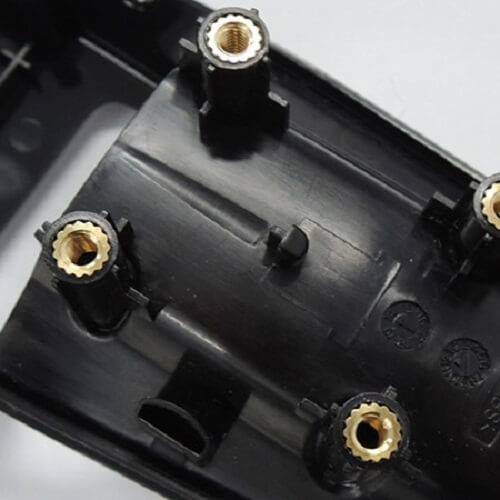
INSERT INJECTION MOLD
產品分類 : 射出模具
INSERT MOLDING TECHNOLOGY: When a metal, plastic or ceramic part needs to be embedded in plastic to improve product structure it is called Insert Molding. It is a widely used process and one that YOMURA TECHNOLOGIES specializes in. With Insert Molding, a part is placed in a mold cavity then a selected plastic material is injected directly over it resulting is a single part with the insert(s) encapsulated by the material. This process normally uses engineering plastics for improved wear resistance, tensile strength and weight reduction. Insert Molding can be a highly efficient alternative to the assembly of discrete parts using soldering, connectors, fasteners, or adhesives. It also expands plastic capabilities and can reduce final product cost by limiting the amount of costly metal needed to create a part. And importantly, because we can use conventional single shot injection machines for Insert Molding, tooling costs are lower than with a multi-shot processing. Benefits: Reduced assembly and labor costs Because insert molding joins numerous components with thermoplastic, assembly and labor costs are greatly minimized. For example, a single stamping can be overmolded, then perforated to create multiple circuit paths. Reduced size and weight By eliminating fasteners and connectors, and by combining the physical strength of resin and metal inserts, insert molding yields smaller and lighter components. Increased reliability With every part tightly secured in thermoplastic, an insert molded component prevents part loosening, misalignment, improper terminations, and other problems. The thermoplastic resin also provides improved resistance to shock and vibration. Increased design flexibility Designers appreciate the virtually unlimited configurations that insert molding allows. For example, in creating a 3D circuit board, overmolding permits circuitry to move freely through the part, from inside to outside, up walls, down in holes-and the plastic ties it all together. Materials: Engineering plastic or Thermo Plastic Rubber (TPR) inserted with metal frame die casting, plated copper pin, sockets, wire frames, etc. Applications: TPR + Metal Frame(3C Mechanical Parts) ABS + Al. Die Cast (Sports/ Medical) Eng. Plastic + Patting Pin/Eng. Plastic + Wireframe (Connector) Eng. Plastic + Copper Pin/Contact (Precision Electronic Component)
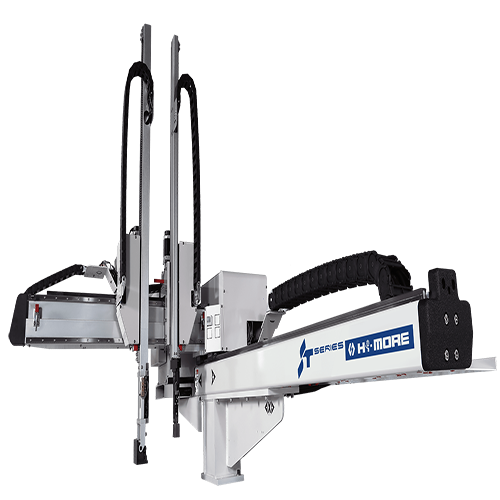
ST-800 / 900
產品分類 : 工業機器人
.整體結構設計改良 造就輕盈機身 .相較THS系列 重量減少20KG .與HX系列比較 減輕將近10KG .輕量化機身 大幅減輕馬達負荷 & 增加壽命性能