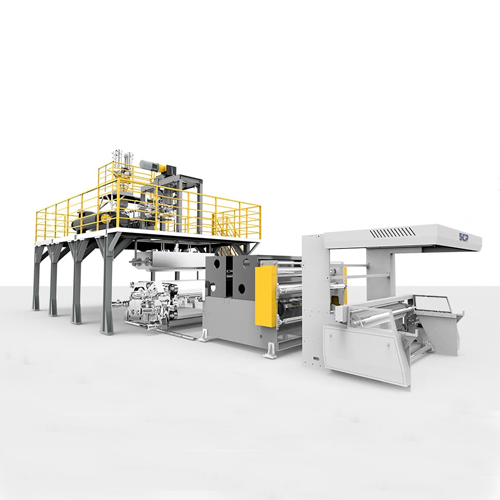
SCP-MB1600
產品分類 : 長絲與紗線押出生產線
Meltblown Non-Woven Fabric Production Lines - MB1600 Using extremely fine fibers to produce meltblown Non-Woven Fabric
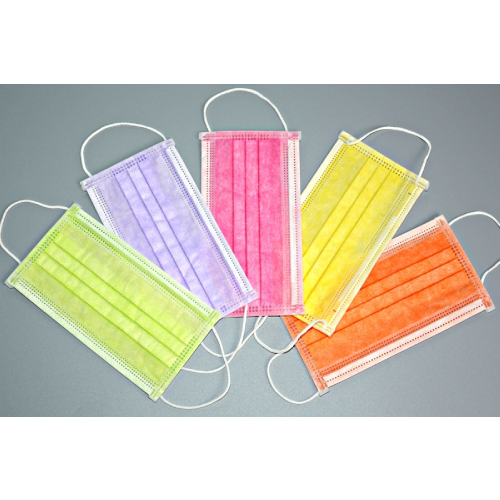
電暈靜電駐極設備
產品分類 : 不織布產線
This CORONA ELECTROSTATIC TREATER is used to turn materials such as melt-blown fabric (face mask sheet),non-woven fabric (non-woven sheet) and polymers into electrets. The equipment includes a high-frequency inverter power supply, special electrodes and rollers. Through the mutual control of these components, the electret material can deeply capture the charge energy, and maintaining the polarization for a long period. This equipment can be used for application such as turning melt-blown fabric, non-woven fabric (non-woven fabric) and air filter into electret. It greatly increases the filtration efficiency of the filter material by capturing tiny particle which is smaller than filter density. More importantly, this CORONA ELECTROSTATIC TREATER helps melt blown fabric increase 45~65% of filtration efficiency and turns it to the most important layer for medical face mask such as N95, KN95 etc. to reduce infected by corona virus COVID-19. Note: An electret is a material that almost remains electric polarization permanently and is able to generate an electric field in the surrounding area. The electret strength will last longer when corona electrostatic charges deeply by high voltage and frequency.
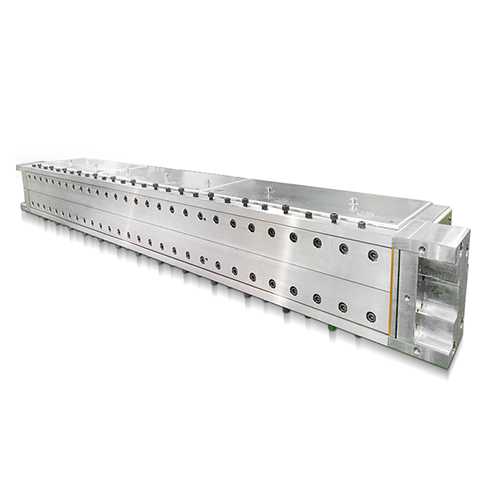
熔噴模具
產品分類 : 押出模頭
SUITABLE AVAILABLE FOR POLYMERS INCLUDING PET And PP High processing precision. Internal heating with heating rod, external heating with heating board, temperature control by heating oil cycle to ensure products of good uniformity. Meltblown filter in continuous and automated production to cut production losses more than 35%, cu costs, reliable product quality. Cut production materials consumption sharply. Featuring high yield, low power consumption, low loss, easy operation. Integrated meltblown Extrusion Die. Integrated meltblown Extrusion Die featuring precision aperture, good consistency and without maintenance wear out. Improved meltblown fiber quality and uniformity, improved product quality. Improved Extrusion Die life cycle and life span. Reduced Extrusion Die change operating time, cut maintenance cost and power consumption. Installation capacity down 30 ~ 40 KW. Cut production costs sharply.